aquatherm blue
Piping system for air conditioning, heating and refrigeration, and plant engineering __
aquatherm blue represents a new standard in commercial and industrial piping systems.
Aquatherm Blue Advantages
-
Corrosion-free
aquatherm blue is hydrophobic, meaning it will never corrode or scale, even after decades of use. This results in high efficiency, consistent performance, and low pumping costs year after year. -
Heat-fusion connections
Properly preformed heat fusion connections form a permanent, leak-free connection, and no solder, solvents, or glues are ever used. -
Excellent flow rate
-
Long-lasting
Properly applied and installed aquatherm blue has an anticipated lifespan of 50+ years. -
Lightweight
Durable aquatherm blue is much lighter (up to 70%) than similarly sized steel pipe, making it safer to work with. -
Fully recyclable
aquatherm blue is fully recyclable at the end of its long life, and directly qualifies for LEED credits. -
Multi-layer faser-composite technology
Faser-composite technology minimizes linear thermal expansion by 75%, ensuring long life and simplifying direct-buried applications. -
Available sizes from ½" to 24".
A wide range of pipe sizes and fittings means aquatherm blue can handle any size commercial heating and cooling.
Designing with aquatherm blue
Aquatherm's pipes are manufactured using a standard dimension ratio (SDR), meaning the wall thickness is a ratio of the total diameter. This is different from schedules, which are commonly used in North America, but is typical of fusible plastics. As a result, all pipe sizes in a given SDR have the same pressure ratings. The ratings do not decrease with larger size SDR pipe as they do with schedule-based pipe.
Each SDR provides its own advantages. The SDR is one of the major factors used in engineering an Aquatherm piping system for a specific application.
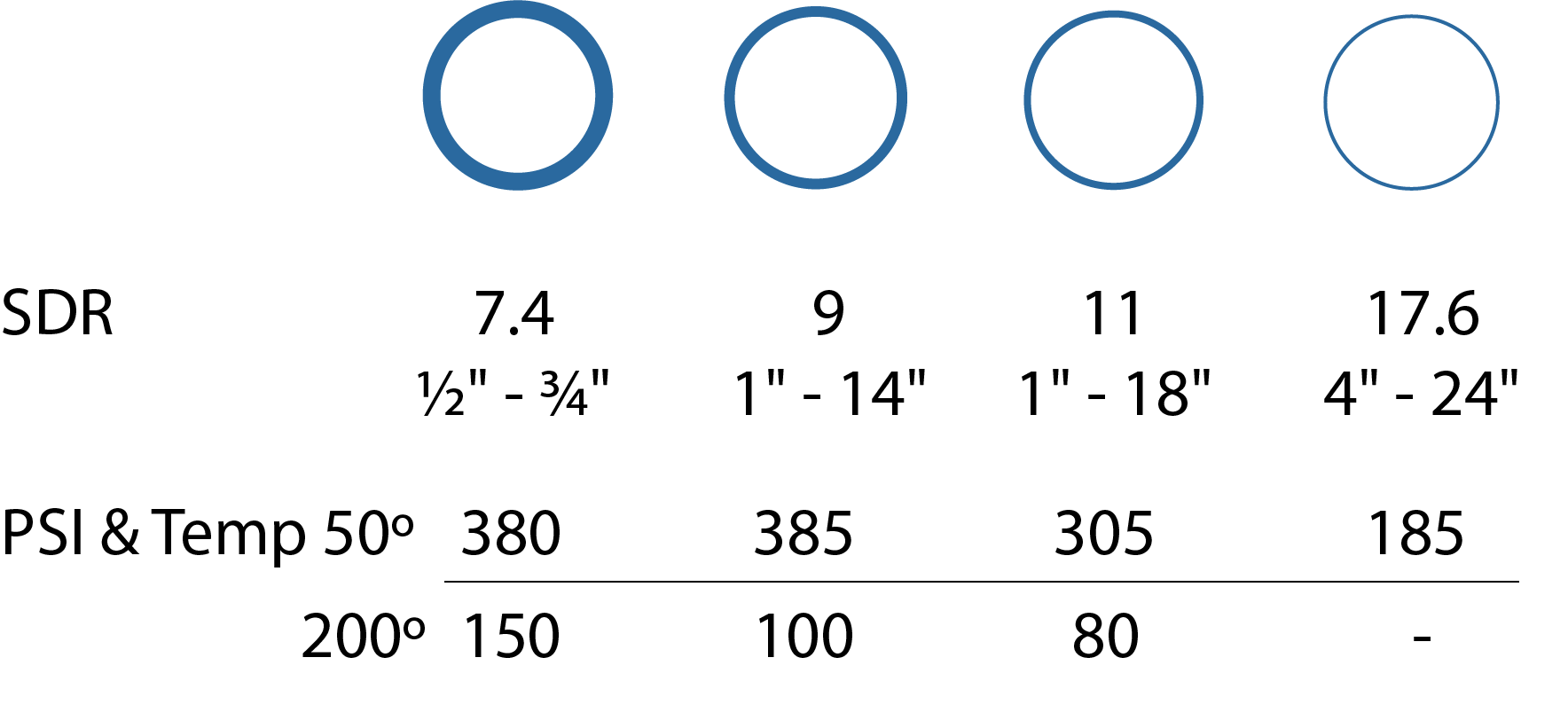
aquatherm blue pipe comes in a wide range of sizes and thicknesses to adapt to your project.
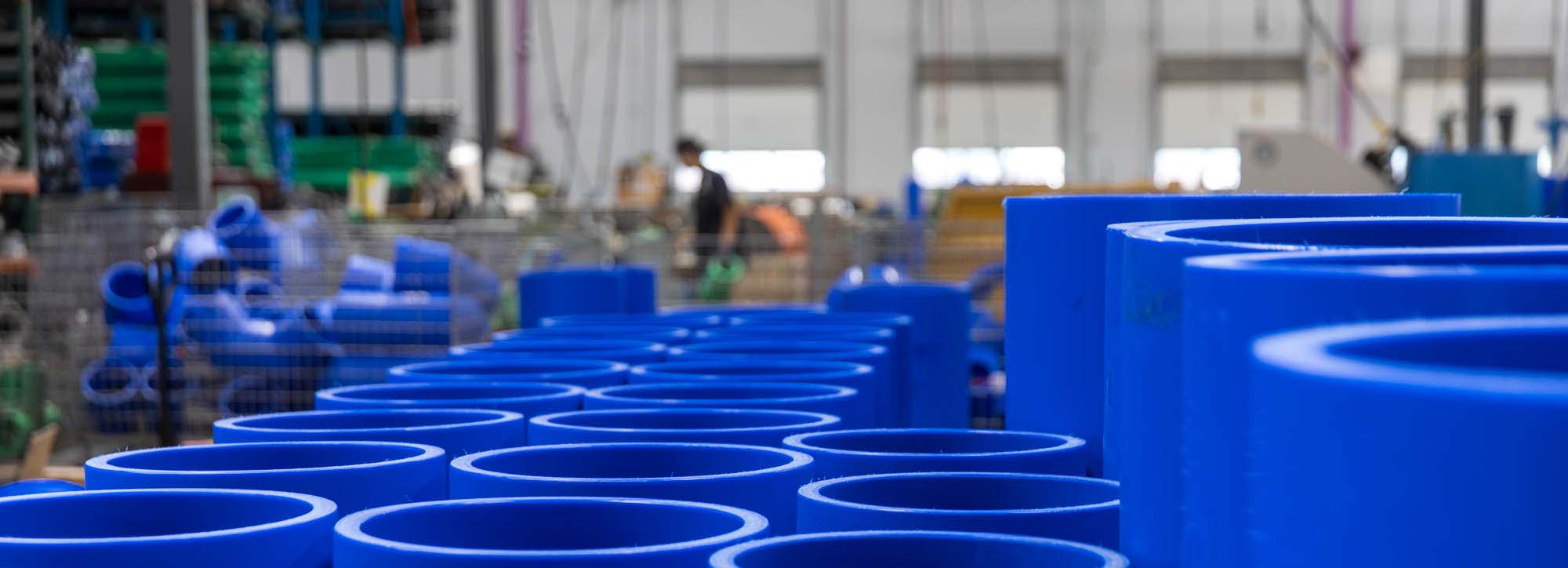
Approvals
NSF 14 | ICC | ASTM F 2389 | IAPMO | UMC | IMC | CSA B137.11
aquatherm blue has been tested and approved according to all major industry standards
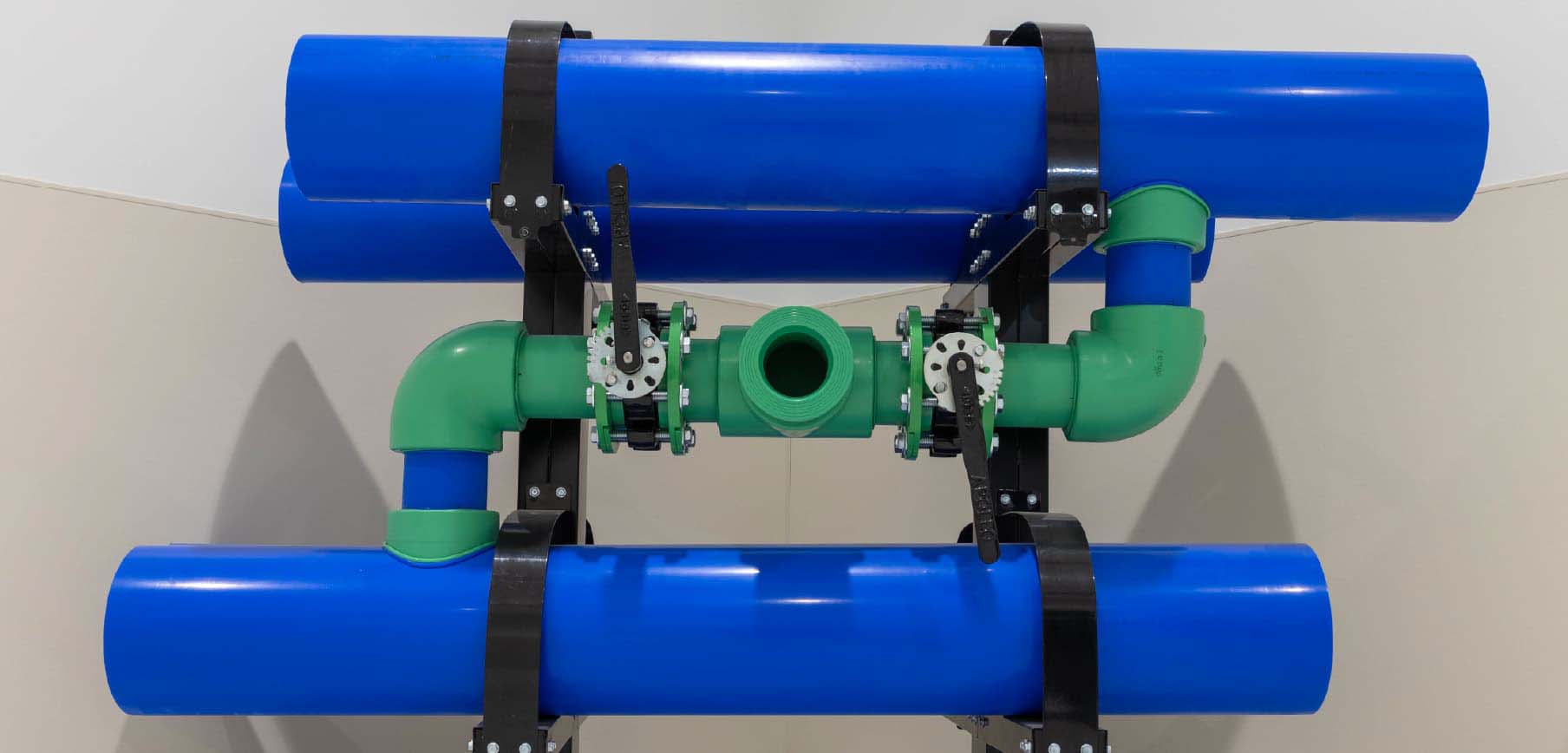
Applications
-
Heating Distribution
For commercial, industrial and residential use, aquatherm blue pipe with multi-layer, faser-composite (MF) is an ideal choice due to its reduced linear expansion and resistance to corrosion, which increase performance and extend service life. Non-faser coils are also available for use in snow-melt applications in concrete or asphalt. -
Heating Distribution
For residential, commercial and industrial use, aquatherm blue pipe has a natural insulation value that helps reduce heat gain and often eliminates problems with condensation, making it an excellent choice for cooling towers and condenser water. -
Industrial Applications
For the processing and transport of aggressive mediums and materials, aquatherm blue pipe resist many types of chemicals. -
Radiant Heating Systems
Aquatherm's fused connections, low pressure drops and 8-to-1 bending radius (non-MF only) make for a safe and efficient installation. Aquatherm's fusion outlets allow for an extended manifold layout, which helps reduce costs and improve performance. -
Geothermal
While all Aquatherm pipe can be safely buried in soil, sand or concrete, aquatherm blue pipe is available in larger diameters and has heat stabilization, making it a perfect match for geothermal applications. Aquatherm pipe is also suitable for directional boring. -
Condenser Water Systems
aquatherm blue pipe is able to withstand the more corrosive environment of open loop condenser water systems, where higher dissolved gas concentrations are found in the water, and more aggressive treatment chemicals may be needed for prevention of bacterial growth such as Legionella.
Design Resources
Installing aquatherm blue
Fusion Process
Heat fusion is a process used to join thermoplastics such as aquatherm's polypropylene together. Rather than using glue, solder, or a mechanical connection and gasket, heat fusion physically turns the two pieces of plastic into one piece.
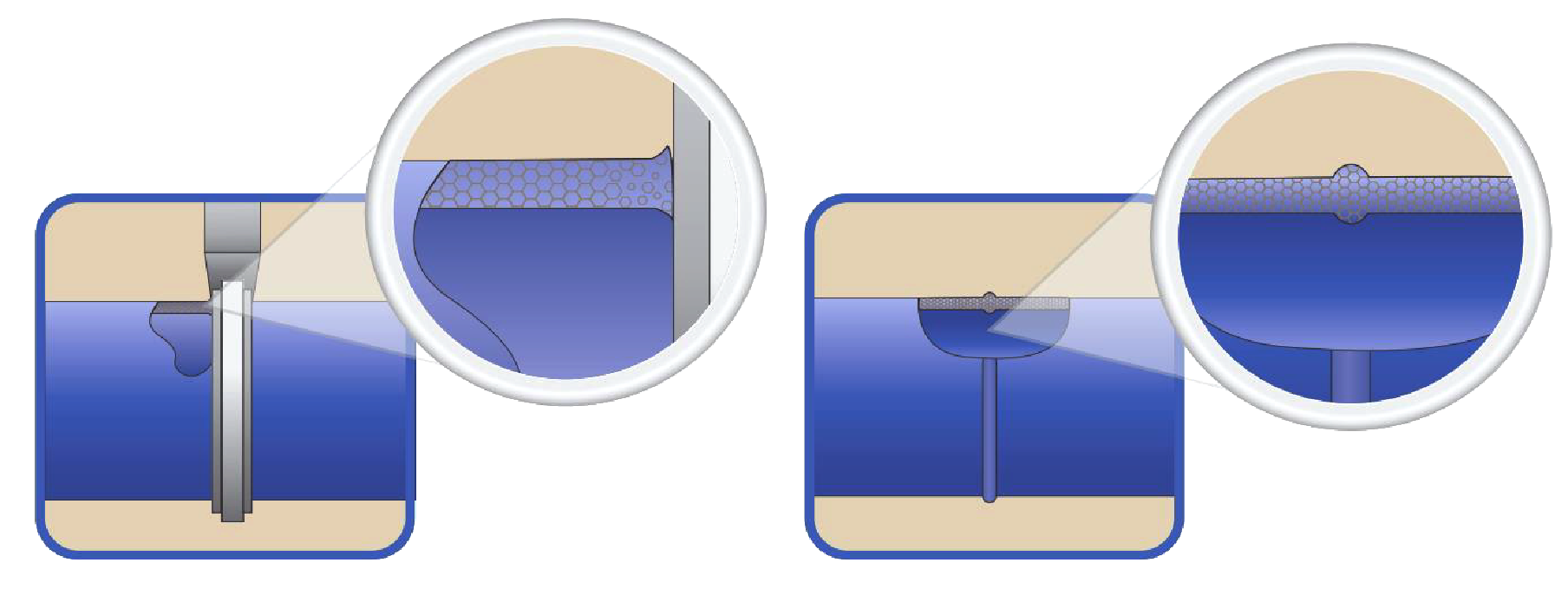
Heat fusion works by returning the connection point to a melted state, the way it was during production. This allows the polypropylene chains to join together as the connection cools for a permanent bond, as if they were manufactured as one piece. This prevents any sort of chemical or physical weakness at the point of connection and results in a much lower instance of leaks or failures.
Types of fusions:
Tool Options
As a pipe manufacturer, we do not produce the fusion tools ourselves. We rely on tool partners to provide the various tools you will need to weld our products.
In working with our products, you will need to have fusion tools on hand to install. You can choose to rent or purchase the tools.
Here are our preferred tool providers:
Installation Resources
aquatherm blue on the Ground
Featured Project
Other Projects
-
memoryData Centers
-
schoolUniversities
-
local_shippingIndustrial
Made from our proprietary polypropylene resin, aquatherm blue is ideal for pressure piping heating and cooling systems in commercial and high-rise residential buildings, schools and universities, data centers, hotels, hospitals and government buildings, as well as process cooling systems in industrial and manufacturing plants.
aquatherm blue Longevity
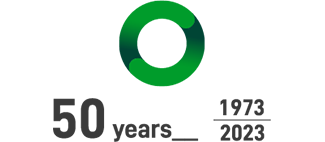
Aquatherm Blue incorporates 50 years of German innovation and engineering to create the safest, cleanest, longest lasting, and highest performing piping systems available.
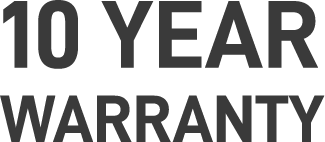
Aquatherm Blue is supported by an extensive ten-year warranty that covers any parts, labor, personal injury, and incidental damages caused by material failure due to manufacturer defect. The warranty covers the pipes, fittings, and damages up to €20 million per event.