Electrofusion Couplings
201603A – AQTTB
Date Issued: 29 March 2016
Electrofusion is another technique for joining Aquatherm pipe (PP-R, RP(RCT))2. It entails using a coupling that is wound with heating element wires embedded in PP-R, which can be slipped over two ends of pipes to be joined. An electrical current is applied to the coupling causing heat to be generated in the coils, melting the PPR of the coupling and the pipe together, forming the fusion bond.
The installer manual has several pages dedicated to the proper steps to be taken in making an electrofusion connection. The purpose of this bulletin is to give a little more detail into the preparation, process and expected results of electrofusion couplings.
Electrofusion couplings can be used in some cases where normal fusion equipment cannot be used because of space or height restrictions or when making a final connection in a small space where the rest of the piping is already rigidly in place.
The first and most important step in making a correct electrofusion connection is to ensure that the pipe ends to be joined are cut square and perpendicular to the length of the pipe. Some cutters will depress the ends of the pipe when cutting. This also happens when the cutter is dull. This is called conical collapsing. If the conical collapsing is enough to cause the pipe to not make contact with the heater spirals, the joint will be insufficient and may fail.
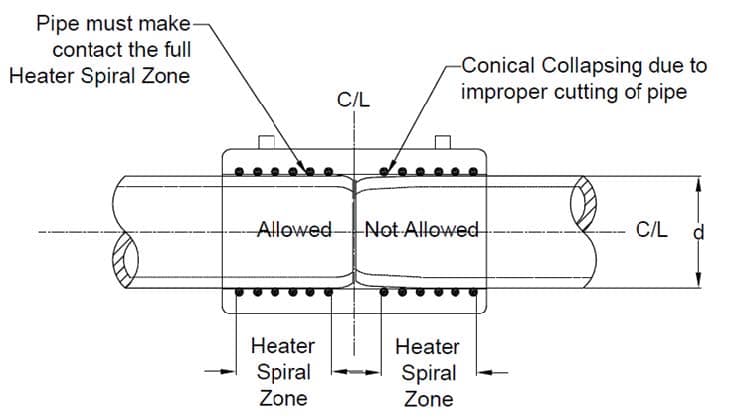
Figure 1: Proper cutting of the pipe is essential to good fusion
If conical depression is occurring, use another method of cutting the pipe or sharpen the cutter.
The out-of-roundness of the pipe should not exceed 1.5% of the pipe outside diameter or a maximum of 3 mm, 0.118 inches in the welding area. If the pipe exceeds this, then rounding tools or circumferential clamps may be necessary to keep the pipe within the tolerance during the electrofusion process.
After the pipe is cut the next step is to peel the pipe. Peeling the pipe involves removing some of the exterior of the pipe material to allow the pipe to be smoothly inserted into the electrofusion coupling. A rotating peeling device with a constant wall thickness removal should be employed. The tool should remove approximately 0.2 mm or 0.008 inches of the exterior of the pipe on each pass. Peeling should be done only in the area of the heating spiral zone, or the area to be covered by the coupling itself.
The pipe must be de-burred on the inside and the outside. All chips must be removed without touching the surface of the peeled area with your fingers. If the peeled area is contaminated after the peeling process, the area should be thoroughly cleaned with isopropyl alcohol or additional cleaning may be required. As a precaution the final peeled area should always be thoroughly cleaned with isopropyl alcohol. It is critical that the bond areas of the peeled pipe and fitting socket are clean and not contaminated prior to doing the weld.
A mark should be made on the pipe to represent the intended insertion point of the pipe into the coupling. The fitting must not be tilted or pushed onto the pipe end with force. Certainly it is not advisable to use anything but manual pushing to get the fitting onto the pipe (i.e. NO HAMMERS!). If the fitting will not slip easily onto the pipe another pass should be made with the peeling tool.
The pipe and the fitting must be at the same temperature at the time of fusing.
Each Aquatherm electrofusion coupling is tagged with the required voltage and time for which that voltage should be applied. Each coupling should remain in its plastic wrapping until just before the coupling is to be installed. The electrical connections on the fitting must be easily accessible.
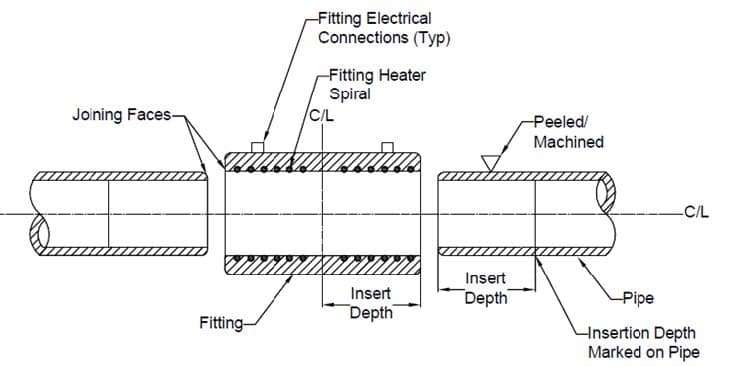
Figure 2: Electrofusion coupling preparation
Figure 3: Completed electrofusion coupling
Cables connect the welding device to the electrofusion coupling. Be sure that these cables are clean and free from debris at the point of connection with the electrical fittings on the coupling. The welding device obtains the data to perform the welding by using a bar code that is printed on the electrofusion coupling tag. If the bar code is missing or unreadable the pertinent information may be input into the device manually. Ensure that the displayed data on the device matches the data on the coupling.
In the event of a power failure or other interruption of the welding process, the welding procedure may be re-started on one occasion, assuming that there are no other defects on the fitting or the welding device. It is necessary that the fitting be completely cooled the entire required cooling period before attempting to repeat the procedure.
The cables may be removed from the coupling electrodes as soon as the welding time has been achieved and the device is switched off. Allow the coupling and the pipe to completely cool the required times before moving or applying pressure to the joint.
It is important to remember that electrofusion couplings can only be pressurized to a maximum of 300 psi.
For more information, refer to DIN DVS 2207-1 Standard for Butt Fusion Welding.
Aquatherm Electro-Fusion Coupling Requirements
Electrofusion pin size = 4 mm2
Revisions
- 7 February 2017 Added Electro-Fusion Coupling Requirements Table
- 10 September 2021 – Added RP(RCT) and electrofusion pin size