COLD RING SOCKET FUSION
TECHNICAL BULLETIN: 201603B-AQTTB
Date Issued: 29 March 2016
Aquatherm does not endorse the use of the cold ring and chamfer tools, but if their use is desired, Aquatherm does not object. The following are proper procedures for using the chamfer and cold ring tools for socket fusion.
The chamfer tool is put on the end of the pipe and turned. This cuts a chamfer on the end of the pipe which reduces the force necessary to insert the pipe, and also reduces the size of the material bead on the interior of the socket.
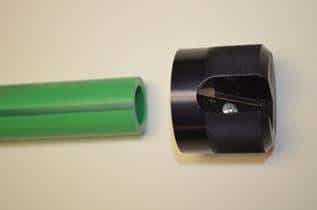
Chamfer tool and pipe
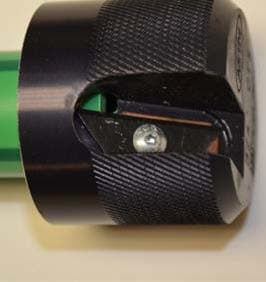
Chamfer tool
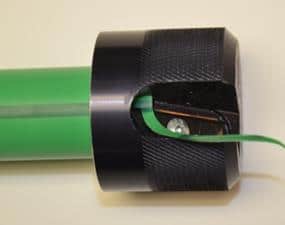
Chamfer tool in action
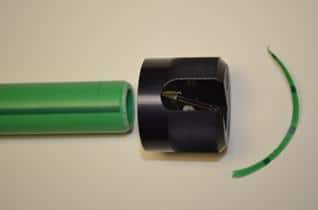
Chamfered pipe, chamfer tool, chamfer scrap
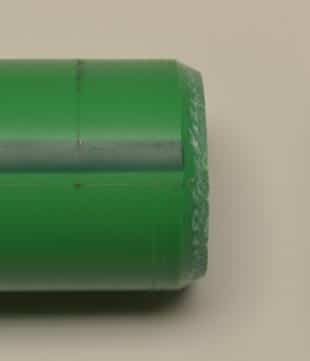
Chamfered pipe end
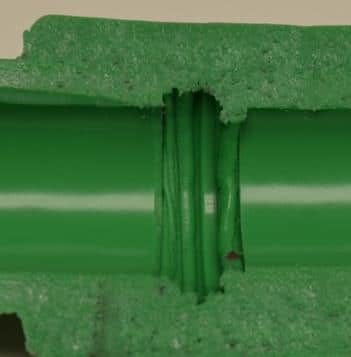
Pipe section showing lack of interior material bead
The chamfer tool is designed to be the proper length for insertion of the pipe into the socket. This allows the chamfer tool to be used to determine where to attach the cold ring tool. Use of the cold ring eliminates the need to mark the pipe with a depth gauge.
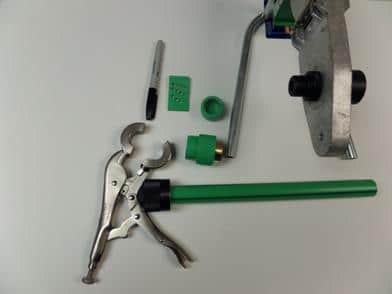
Cold Ring, Chamfer tool, Heating Iron and fittings
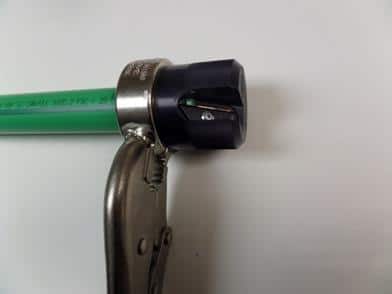
Cold Ring applied to the pipe at the base of the chamfer tool.
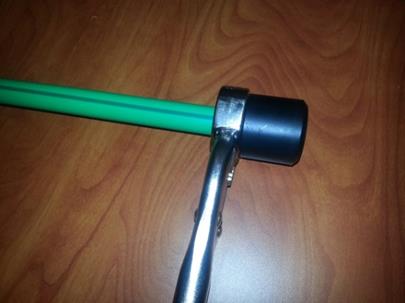
Cold Ring Attached to the pipe
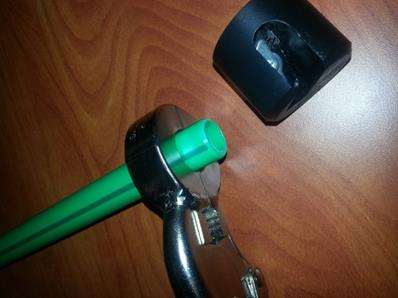
Removing the Chamfer tool, the pipe is ready to be heated
The cold ring tool is then used to hold the pipe while inserting the pipe into the fusion head.
The heating tool is applied to the pipe until it hits the cold ring
When the socket joint is completed, the results are:
- A flat bead at the socket face with two small material protrusions on opposite sides where the jaws of the cold ring tool meet when clamped on the pipe.
- A uniform insertion of the pipe
- And straight alignment of the pipe
Flat fusion bead from use of cold ring.
Because Aquatherm pipe is rigid enough to reliably maintain its shape during socket fusion without the additional support offered by the cold ring, the use of these tools is optional. Chamfering Aquatherm pipe to achieve a smaller internal bead has not been shown to yield a significant reduction in system head loss. The use of cold ring and chamfer tools with Aquatherm pipe may help installers to more quickly and reliably make good and properly aligned socket fusion welds, and has not been observed to be detrimental to the integrity of the bonds created in the socket fusion process. Because the use of these tools produces a single flattened bead instead of the rounded double bead normally expected of a proper socket fusion weld, it is still important that the insertion depth be marked on the pipe in order to serve as a visual indication that a good weld has been made.