aquatherm fits like a glove at massive ohio manufacturing plant
More than half a million square feet, 15,000 feet of Aquatherm piping, 3.6 billion nitrile gloves annually . . . everything about the American Nitrile warehouse-to- manufacturing-plant conversion is big.
The Challenge
A 527,000 sq.ft. warehouse was on a fast-track conversion to a manufacturing plant, and needed an extensive piping system to handle its vital process cooling needs.
The Solution
Aquatherm PP-RCT pipe fit the bill, as it allowed fast fabrication and installation and easy overhead mounting throughout the massive space.
When we say that Aquatherm pipe can handle commercial heating and cooling and industrial process cooling projects of any size, we’re not just talking. For proof, look no further than the American Nitrile plant in Grove City, OH, a suburb of Columbus. Aquatherm pipe in sizes up to 24-in. is playing an integral role in the conversion of a 527,000 sq. ft. warehouse into a factory that will produce medical and non-medical latex-free gloves. A LOT of gloves: 3.6 billion annually when the plant is fully operational.
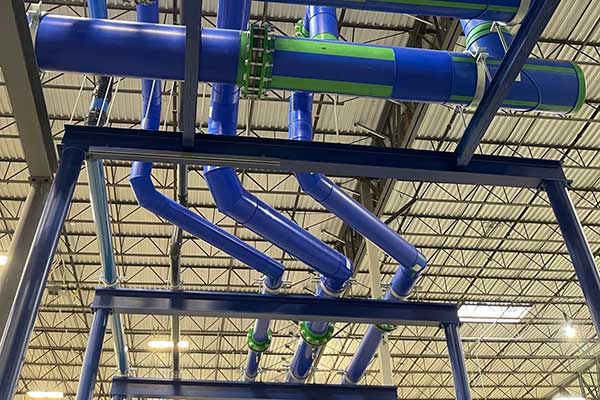
Lightweight, versatile Aquatherm pipe will carry the process cooling water to and from the manufacturing plant’s three chillers.
15,000 ft. of Aquatherm Blue Pipe SDR 17.6 will serve the facility’s chilled-water process loop. The 24-in. pipe is the largest SDR (standard dimension ratio) pipe that Aquatherm manufactures.
American Nitrile engineer Alex Mallison said the process cooling needs of this plant are extensive: about 750,000 gallons of water each day. That’s because the proper cooling of the material makes the difference between a high-quality nitrile-based liquid and a “ball of goo.”
“Very simplistically, in this process we’re taking a solid that’s suspended in water, getting it to stick to a ceramic mold in the shape of a hand, and then heating it to remove all the water and other aqueous chemicals,” Mallison explained. “The cooling is necessary as the mold passes through three nitrile dipping tanks. If we didn’t have that cooling, our nitrile would take on a gel-like consistency instead of being a nice, smooth, almost water-like substance.”
Mallison noted that for every 10 gallons of water brought into the facility, he can recycle four gallons directly back into the process. The other six gallons are treated in an internal state-of-the art wastewater facility before being discharged to the city.
The Aquatherm pipe carrying all that cooling water includes 24-in. pipe for the mains, 12-in and 14-in. for the supplies and returns, and 4-in. and down for the connections to the machines. The supply water in the open-loop system will be cooled to 55ºF and will run at 60 psi. The return water will be at approximately 70ºF and pressurized to about 40 psi. The condensing water will be 85ºF to 110ºF depending on the time of year, and the cooling towers will run all year at 40 psi.
Other key components of the process cooling system at American Nitrile include three Daikin chillers with a combined 2,250 tons of capacity, Marley cooling towers, and Grundfos pumps.
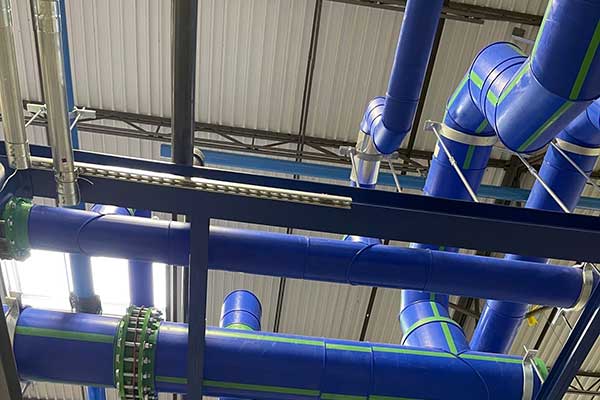
The Aquatherm pipe at the American Nitrile manufacturing plant in Grove City, OH, was fabricated on-site by the skilled team from the Columbus branch of Sauer Group LLC.
COUNTNG UP AQUATHERM’S BENEFITS
Mallison had spec’d Aquatherm pipe on other successful projects, and said there were several important factors for its selection at American Nitrile.
“We put a lot of thought into which piping system made the most sense for a project this large and complex,” he said. “I personally hate doing chilled water/cooling tower systems in carbon steel because of the amount of debris that can build up in the system and how quickly those pipes can corrode.”
American Nitrile’s founder and CEO, Jacob Block, was eager to get the factory up and running, and the project ran on a tight schedule. Aquatherm was a natural choice here. The heat fusion process used to join Aquatherm pipe requires no welding, open flame, or fire watch, is much faster than welding steel, and creates virtually leak-free connections.
“You basically set up the fusion machine and you can weld four pieces of 24-in. piping in a single day,” Mallison said. “A good stick welder might be able to complete one weld in that time. So the time savings [of the installation] were significant.”
The light weight and ease of working with the Aquatherm pipe also impressed the union pipefitters on the job—20 of whom Mallison had trained specifically for this project. They particularly appreciated that, depending on the size and SDR of the pipe, Aquatherm is up to 70 percent lighter than carbon steel pipe.
“The craziest thing is watching a guy lift a 24-in. tee above his head,” Mallison said. “You just can’t do that with metal, which is heavy, bulky, and hard to work with. These guys are working their tails off for us here, so if there’s something we can do to make their jobs easier and safer, we’re going to do it.”
In addition, unlike metal pipe, Aquatherm is hydrophobic and will never scale or corrode, so the flow rate when the pipe is new will remain the flow rate throughout its long service life.
The clincher for spec’ing Aquatherm came when Mallison contacted his long-time Aquatherm distributor in central Ohio, Pipe Valves, Inc., a leading independent industrial PVF supplier in the Midwest. The distributor assured him that it could easily supply everything the American Nitrile project needed.
“We created a parts list for Pipe Valves, and they had almost everything we needed already in their possession,” Mallison said. “What they didn’t have they were able to obtain and ship directly to the facility within a week or two, and we were off to the races.”
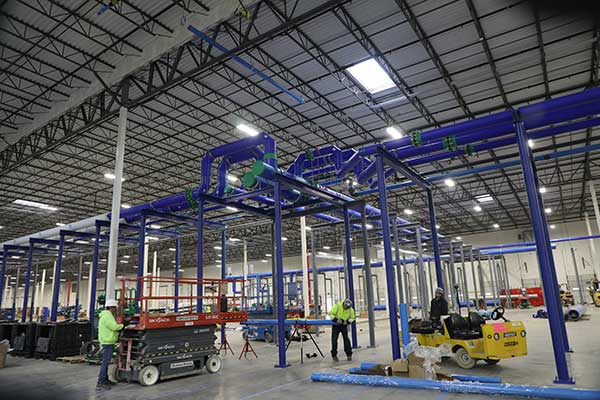
More than half a million square feet, 15,000 feet of Aquatherm piping, 3.6 billion nitrile gloves annually . . . everything about the American Nitrile warehouse-to-manufacturing-plant conversion is big.
A COMMITMENT TO SUCCESS
At the Columbus branch of Sauer Group LLC, Claire Green, design/build manager, and Dave Koch, general foreman, drew on their company’s experience with other polypropylene piping installations. At American Nitrile, the size of the project, its fast timeline, and some miscommunication related to tooling and training led to some challenges early on. However, everyone involved in the project from the Sauer Group, Aquatherm, Pipe Valves, and American Nitrile pulled together to ensure the project’s success—and to meet the code of excellence set forth in the Sauer Group’s union contract.
Sauer availed itself of Aquatherm’s Scan-to-Fab service in the mechanical room, and had some custom fabrication done at Aquatherm’s U.S. headquarters in Utah, but overall performed the vast majority of the fabrication onsite using a combination of McElroy and Widos fusion machines.
“We installed significant lengths of pipe—three lines that are about 750 feet each—with just four guys in an incredibly short amount of time,” Koch said. “Aquatherm is light, easy to handle and work with, and it goes in remarkably fast, especially on long, straight runs.”
As the American Nitrile project nears completion, Koch said he and Green find themselves considering other projects where Aquatherm pipe would work well.
“Aquatherm is a good product and I would look forward to using it again on other jobsites,” Koch said. “Claire and I have talked about specific locations and applications that this product would be great for.”
Green added that although the company had experience in polypropylene piping installations, the opportunity to hone their skills with Aquatherm pipe on a project of this size presented a great opportunity for the Sauer team.
“We have a fantastic crew here and we’re always open to new technologies and alternative solutions,” she said. “Aquatherm is a great tool to have in our tool belt.”