THE FOLLOW-UP FILES: AQUATHERM STANDS THE TEST OF TIME IN CHEMICAL TRANSPORT APPLICATION
Webb Chemical Service Corp. has been in business for nearly 60 years, and the company’s long and successful history and ongoing growth have always been buttressed by its commitments to quality and the environment.
The Challenge
Webb Chemical was looking for a long-term solution to transport high-quality chemicals safely at its repackaging and distribution facility
The Solution
Chemically inert and durable aquatherm polypropylene pipe has been providing flawless and leak-free chemical transport at Webb Chemical for seven-plus years
Webb Chemical Service Corp. has been in business for nearly 60 years, and the company’s long and successful history and ongoing growth have always been buttressed by its commitments to quality and the environment.

Webb Chemical Service Corp. in Muskegon, MI.
Those commitments guided the company in 2012 when it selected to aquatherm pipe for chemical transport at its chemical repackaging and distribution facility in Muskegon, MI. The company’s goals were safety—leak-free performance was a must—and ensuring the purity of the chemicals that were being packaged and provided to customers. Those goals have been met for more than seven drama-free years. (To read the original case study, please visit https://aquatherm.com/case-studies/pp-r-pipe-system-endures-crazy-drummer-and-caustic-chemicals-at-tank-farm.)
Webb provides commodity chemicals to a huge variety of industries including industrial, pharmaceutical, household, agricultural, aerospace, and many others throughout the U.S. These chemicals include ethylene glycol, propylene glycol, caustic potash, caustic soda, sodium bisulfate, and phosphoric acid, and Webb worked closely with aquatherm upfront to ensure aquatherm’s compatibility with the various fluids.
A PRE-INSTALLATION EVALUATION
The actual behavior of any piping system when exposed to a specific chemical is dependent on the exposure conditions (temperature, pressure, flow, duration, etc.), the stresses on the piping material, and system (mechanical, thermal, cyclic, etc.), and the ancillary materials in the system (O-rings, seals, gaskets, metal components, etc.). Therefore, aquatherm evaluates each installation for chemical applications on a case-by-case basis and approved usage of the pipe system.
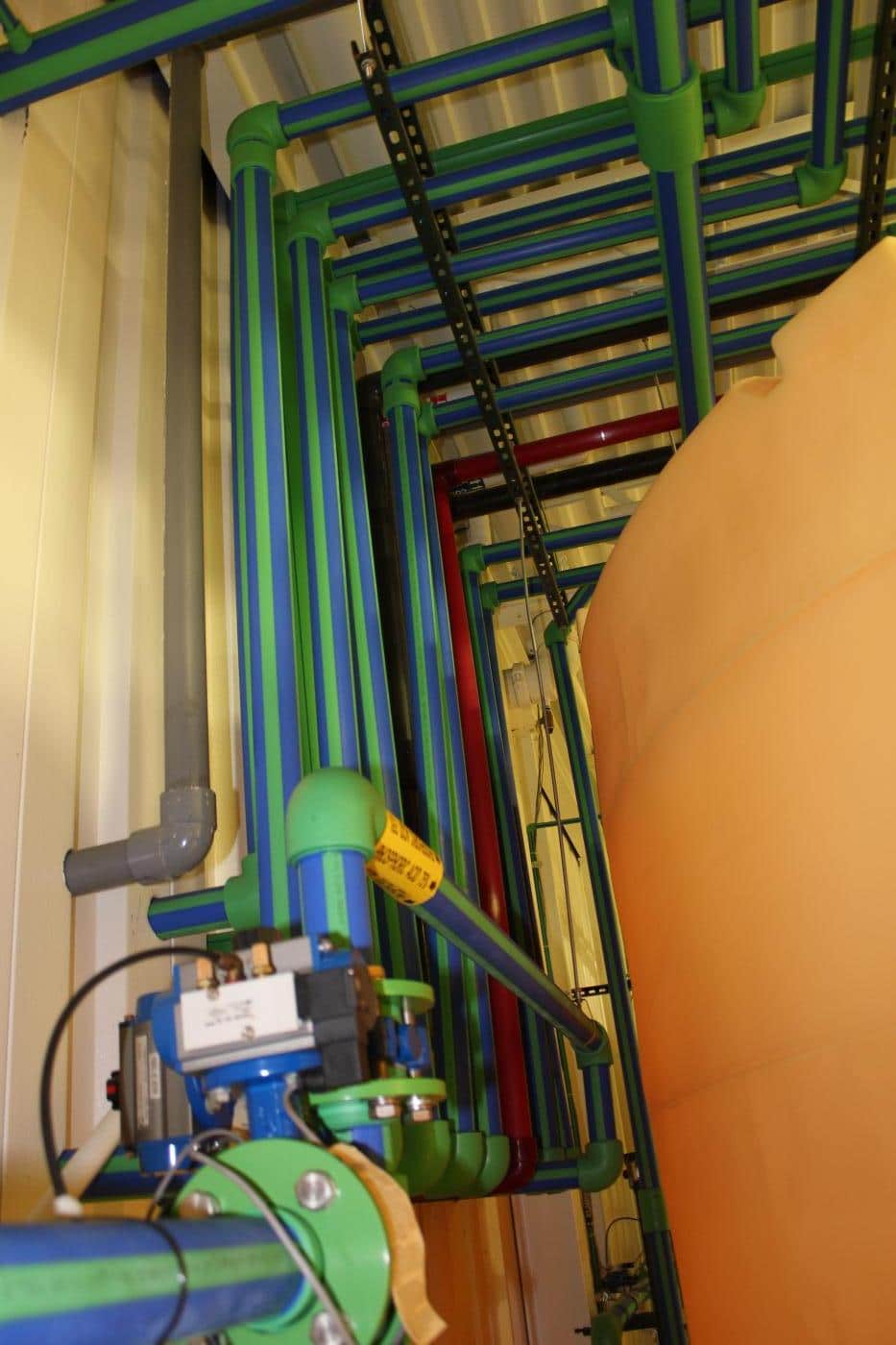
aquatherm pipe in place at Webb Chemical Service Corp.
The installing contractor, Brett Lascko, owner of Lascko Services, provided to aquatherm a list of chemicals that would need to be carried in the pipe, and found out within 24 hours that aquatherm would be suitable for 12 of Webb’s 18 storage tanks, each of which holds 18,700 gallons.
THE IDEAL MATERIAL FOR CHEMICAL TRANSPORT
The chemically inert nature of aquatherm polypropylene (PP) pipe makes it an ideal material for carrying many types of chemicals, and aquatherm’s heat-fusion technique eliminates systemic weaknesses and leak paths in the pipe system. The heat-fused joints maintain the same properties as the pipe itself, so physical stresses will not compromise their integrity. Additionally, aquatherm’s multi-layer, faser- composite layer reduces thermal expansion by up to 75 percent compared to other plastics, and allows the pipe to withstand constant temperatures up to 180°F at 100 psi.
Lascko and his team of nearly a dozen installers took the half-day aquatherm factory certified training course from Columbia Pipe & Supply and began the process of preparing for the installation. The contractor bought a McElroy Spider™ 125 socket fusion welding tool that connects 1-in. to 4-in. pipe and fittings specifically for this project.
THE INSTALLATION GETS UNDER WAY
In October 2012 Lascko employees began installing aquatherm green® and aquatherm blue® in diameters including ½-in., 2-in., and 3-in. to connect the tanks and supply valves located outside the facility where tankers connect. The ½-in. pipe was used for drain lines. In total on the first job, Lascko installed approximately:
3,000 feet of 2-in. multi-layer, faser-composite green SDR 7.4 and blue SDR 11
700 feet of 3-in. multi-layer, faser-composite blue SDR 11
700 feet of ¾-in. multi-layer, faser-composite blue SDR 7.4
338 feet of ½-in. multi-layer, faser-composite green SDR 7.4
338 feet of 1-in. multi-layer, faser-composite green SDR 7.4
169 feet of 1½-in. multi-layer, faser-composite blue SDR 11
The system design at Webb Chemical includes air-operated double-diaphragm pumps, which by their nature create a degree of “hammer” or “chugging” when in operation. However, after seven years in service aquatherm pipe and its heat-fused joints have performed flawlessly, handling both the chemicals themselves and the vibration of the pumps without leaks.
ALL EXPECTATIONS MET
Webb Chemical Plant Manager Kolin Convertini says the piping system has met all of his expectations for strength, compatibility, and performance over time.
“It’s really a solid product,” Convertini said. “We haven’t had any leaks or other concerns, and we haven’t had any issues with the pipe regarding vibration and hammering with the air-operated diaphragm pumps.”
Although Convertini and Webb Chemical could be considered pioneers of a sort, having installed aquatherm when polypropylene pipe installations of this type were fairly new in North America, their openness to alternatives has paid off.
“We have had some struggles with other piping here over the years,” Convertini said. “For example, we’re dealing with a CPVC line where we’re fighting leaks constantly. But our guys love the aquatherm pipe because they never have to mess with it. It’s basically install it and forget it.”
WARRANTY SETS MINDS AT EASE
Because Lascko Services’ installation team took the aquatherm training course and submitted the proper pressure test documentation, Convertini and Webb Chemical also benefit from aquatherm’s 10-year multimillion dollar warranty.
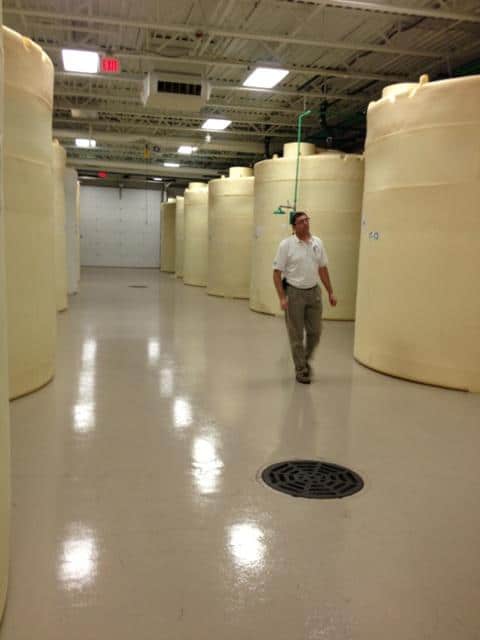
Virtually leak-free aquatherm pipe helps ensure the environment remains immaculate at Webb Chemical Service Corp.
“It’s beneficial when a company puts their name on their product and issues a letter testifying that we can use this product for our application, plus the warranty is one of the things that sets your mind at ease,” Convertini said.
Convertini added that based on his experience over seven years, he would not hesitate to use aquatherm again or to recommend it to operators of other industrial plants who are seeking an alternative piping system.
“Each industrial site has its own unique processes, safety concerns, and hazards,” he noted. “But for us in our process aquatherm has worked great and been basically maintenance-free. Since we installed it, it has performed year after year, and I would definitely recommend it in an application like ours.”